Warehouse demand at record level
Warehouse demand is at record levels. Driven by rising e-commerce demand and related one and two-day shipping demands, the need for new warehouses has never been higher.
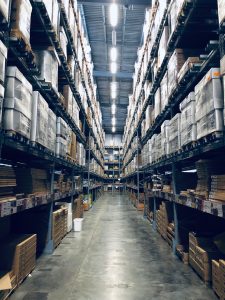
Warehouse demand is at record levels. Driven by rising e-commerce demand and related one and two-day shipping demands, the need for new warehouses has never been higher.
Real estate services firm JLL published a survey of more than 720 logisticians in April that found 74% predicted 5% annual growth or more in warehouse demand over the next three years. About 28% of those said it would be 20% or more, and 71% expected demand from e-commerce to grow significantly through 2024.
That explosion in growth, though, is running into a myriad of factors that are slowing the opening of such facilities, experts said.
“Time is money so every delay in this whole process is adding to the cost, not only for the 3PL (third-party logistics) firms, but also for the customer, and it’s putting additional strain on the supply chain because the capacity can’t be delivered,” said Rock Magnan, president of RK Logistics Group.
A combination of factors, including labor and steel shortages, are forcing delays in getting warehouses up and running, Magnan said.
Enjoying our insights?
Subscribe to our newsletter to keep up with the latest industry trends and developments.
Stay Informed“When we identify a warehouse and negotiate a lease for the building, we are on the hook for the lease cost,” Magnan said. “Unfortunately, if you can’t get the racking, you can’t use the building as you intended to.’’
Mike Ereno, president of Warehouse Engineering and Equipment Services, which designs the interior of warehouses for clients, including RK Logistics, said the global steel shortage is hampering efforts to get storage rack and material handling equipment into new warehouses.
“Most of what we’re seeing here are extremely long lead times for storage rack and material handling equipment,” he said, noting that lead times have moved from four to six weeks to as long as nine months. “There’s issues with sourcing raw materials to get to the mill so they can roll out flat sheets to make their product.”
Ereno also noted that prices are rising — to as much as two and a half times what they were a year ago – and labor shortages at manufacturers are also contributing to delays and uncertainty
Ereno also noted that prices are rising — to as much as two and a half times what they were a year ago – and labor shortages at manufacturers are also contributing to delays and uncertainty. He said the price uncertainty is making it impossible to properly bid out jobs.
Steel prices have risen more than 60% since the start of this year, according to S&P Global Platts. Despite that, some steelmakers are refusing to open older mills.
“The industry is in transition,” Mark Millett, chief executive of Steel Dynamics, told the Wall Street Journal.Cost “If you’ve got ancient assets to compete against new, state-of-the-art facilities, you’ve got to question whether you bring those back.”
The market is also seeing some issues from the semiconductor chip shortage, as all the automation and conveyors require chips, and from rising fuel costs, which are pushing up transportation-related costs.
Both Magnan and Ereno said Amazon is also a factor.
“Amazon has been buying up a bunch of the materials as well,” Magnan said. “They’re the 500-pound gorilla in the room, which is not a bad thing, it’s just a fact. It’s e-commerce, it’s demand for some of the bigger players. All of this is creating a perfect storm that, like Mike said, we haven’t seen in 20 years.”
The market is also seeing some issues from the semiconductor chip shortage, as all the automation and conveyors require chips, and from rising fuel costs, which are pushing up transportation-related costs.
Overall, the perfect storm of issues is forcing the delivery time of warehouses to expand dramatically at a time when more space is needed sooner. Magnan said the time to stand up a facility is typically eight to 12 weeks from the time RK begins engaging with Warehouse Engineering on the interior design. That is now 20 to 24 weeks, Ereno said.
And the outlook doesn’t look good in the short term, Ereno said, adding that he doesn’t see demand for new warehouses dropping much over the next 18 months.
“As long as the demand for space and for warehousing equipment doesn’t decrease, the lead times are not going to come down,” he said. “Everybody is hoping the price of steel comes down, which will at least bring down the price.”